The Main Materials Used in Pneumatic Tubing
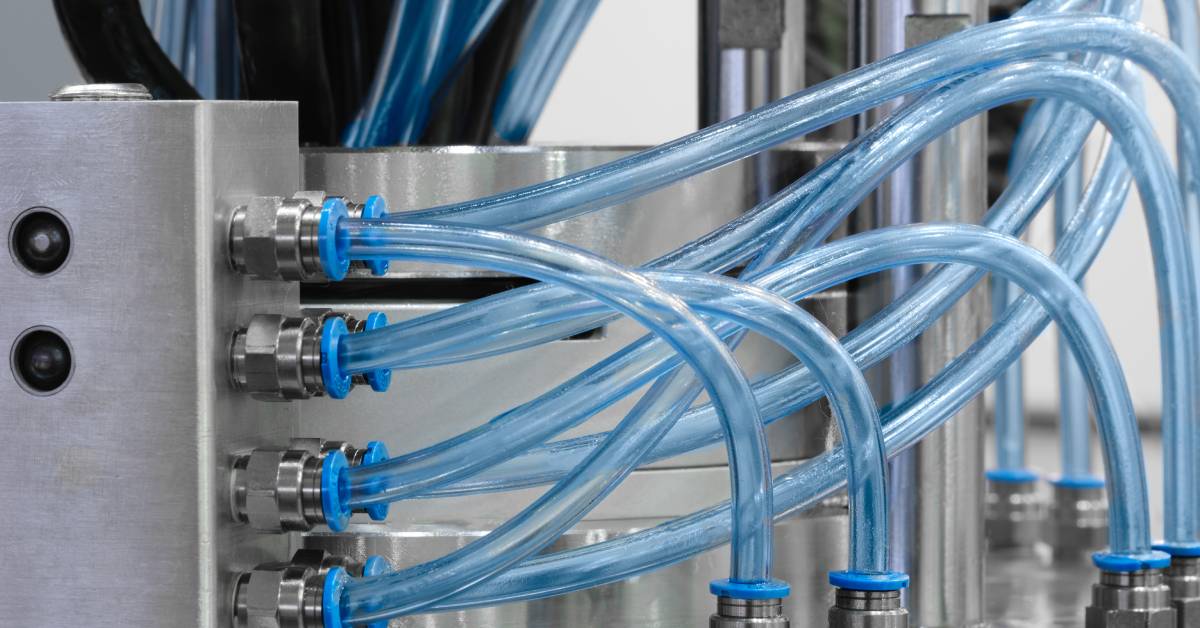
When considering the critical components that make modern machinery and industrial systems function seamlessly, pneumatic tubing often goes unnoticed. Yet, this tubing serves as a vital conduit for pneumatic systems, and the material of this tubing can dictate both the efficiency and durability of your operations.
To make the right decision for your systems, use this guide to the main materials used in pneumatic tubing. Here, you’ll learn the common materials, what they are, why they are great for pneumatic systems, and industry applications in which that specific tubing is used.
The Importance of Material Selection in Pneumatic Tubing
Selecting the right material for pneumatic tubing is crucial because it directly impacts the system's performance, longevity, and safety. Different materials boast unique properties, such as flexibility, resistance to abrasion, chemical resistance, and pressure tolerance.
The proper material selection ensures the tubing can withstand the environmental conditions and operational demands it will encounter. The right material can minimize the risk of failures that could lead to costly downtimes or safety hazards. By choosing the optimal material, you can achieve a balance between cost-effectiveness and operational efficiency, thus ensuring a reliable and long-lasting pneumatic system.
Common Pneumatic Tubing Materials
Polyurethane
Polyurethane is a versatile, flexible plastic material known for its strength, durability, and elasticity. It is an excellent choice for pneumatic systems and tubing due to its superior resistance to abrasion and ability to withstand repeated flexing without sustaining damage.
This material is particularly well-suited for dynamic applications where the tubing may be subject to frequent movements or vibrations. Furthermore, polyurethane offers exceptional chemical resistance, allowing it to perform effectively in environments where it may be exposed to oils, fuels, and certain solvents.
Common Industry Applications for Polyurethane Pneumatic Tubing
- Automation and robotics: Used for air lines in moving parts due to its flexibility and resilience
- Automotive industry: Used in fuel and air lines due to its chemical resistance
- Food and beverage processing: Utilized for fluid transfer, given that some variants are suitable for food-grade use
- Packaging equipment: Applied in machines requiring repetitive motion and flexibility
Nylon
Nylon is a synthetic thermoplastic polymer characterized by excellent mechanical properties, including high tensile strength and resilience. It is widely used in pneumatic tubing and systems due to its superior durability, light weight, and resistance to both abrasion and high temperatures.
Nylon tubing maintains structural integrity even in harsh environmental conditions, making it suitable for various industrial applications. Its smooth inner surface ensures efficient airflow, further enhancing system performance. Additionally, nylon's compatibility with a wide range of chemicals makes it an ideal choice for industries that require chemical-resistant materials.
Common Industry Applications for Nylon Pneumatic Tubing
- Aerospace industry: Used for air systems due to its high tensile strength and lightweight nature
- Material handling: Implemented in conveying systems where durability and abrasion resistance are needed
- Textile industry: Utilized in machinery that operates in high-temperature environments
- Chemical processing: Applied in systems requiring chemical stability and resistance
Polyethylene
Polyethylene is a widely used thermoplastic polymer known for its excellent chemical resistance, flexibility, and low cost. It is a great material due to its ability to withstand various environmental conditions without degrading.
With its smooth interior surface, polyethylene allows for efficient airflow and reduces the risk of clogging or pressure drops in the system. Its flexibility makes installation easy, and its lightweight nature does not add unnecessary weight to the system. Furthermore, polyethylene is non-reactive to most chemicals, making it safe for use in environments prone to chemical exposure.
Common Industry Applications for Polyethylene Pneumatic Tubing
- Agriculture: Used in irrigation systems for distributing water and fertilizers
- Water treatment: Implemented in systems for transferring chemicals and treatment fluids
- HVAC systems: Utilized for air handling and ducting due to its light weight and flexibility
- Medical industry: Applied in equipment to safely carry gases and fluids without contamination
Polypropylene
Polypropylene is a thermoplastic polymer known for its versatility, toughness, and resistance to many chemical solvents, bases, and acids. It stands out as an excellent material due to its high resistance to corrosion, fatigue, and impact.
Additionally, polypropylene is lightweight, making it ideal for systems where minimizing weight is crucial. Its low moisture absorption and resistance to microbial growth make it well-suited for applications in environments where hygiene is essential. Even more so, polypropylene maintains rigidity and performance across a wide temperature range, ensuring reliable operations even in challenging conditions.
Common Industry Applications for Polypropylene Pneumatic Tubing
- Chemical processing: Used for transporting acids and bases due to its chemical resistance
- Pharmaceutical industry: Applied in cleanroom environments where hygiene is vital
- Laboratory equipment: Utilized for fluid and gas transfer without risk of contamination
- Food and beverage industry: Employed in piping systems where lightweight and cleanliness are paramount
Polyvinyl Chloride (PVC)
Polyvinyl chloride, commonly known as PVC, is a versatile thermoplastic polymer renowned for its excellent durability, cost-effectiveness, and resistance to environmental degradation. These qualities make PVC an outstanding choice for pneumatic tubing and systems.
PVC is highly resistant to chemical reactions, which allows it to maintain its integrity even when exposed to acids, alkalis, and corrosive environments. Its inherent flexibility, coupled with robust mechanical strength, makes it suitable for a variety of applications without compromising performance. Furthermore, PVC's easy manufacturability and affordability add to its appeal, making it widely used across various industries.
Common Industry Applications for Polyvinyl Chloride Pneumatic Tubing
- Construction industry: Utilized in plumbing and conduit systems due to its sturdy construction and corrosion resistance
- Healthcare sector: Employed in medical tubing and devices, leveraging its hygienic properties
- Chemical processing: Ideal for transporting hazardous chemicals because of its chemical inertness
- Industrial manufacturing: Used in air and fluid lines, benefiting from its flexibility and cost-effectiveness
Polytetrafluoroethylene (PTFE)
Polytetrafluoroethylene, commonly abbreviated as PTFE, is a synthetic fluoropolymer of tetrafluoroethylene renowned for its exceptional properties. These properties include high-temperature resistance, low friction, and chemical inertness.
PTFE is an outstanding material for tubing due to its ability to withstand a wide range of temperatures without degrading, which ensures reliable performance in extreme conditions. Its non-reactive surface also provides excellent resistance to virtually all chemicals, preventing any interaction with the substances it transports. Moreover, PTFE's low coefficient of friction reduces wear and tear, further enhancing the longevity and efficiency of the pneumatic system.
Common Industry Applications for Polytetrafluoroethylene Pneumatic Tubing
- Aerospace: Used for fuel and hydraulic systems, leveraging its high temperature and abrasion resistance
- Chemical processing: Ideal for transferring aggressive chemicals due to its outstanding chemical resistance
- Pharmaceutical industry: Utilized in environments requiring sterile conditions, thanks to its non-reactive nature
- Food and beverage processing: Applied in systems requiring cleanliness and stability at varying temperatures
Understanding the main materials used in pneumatic tubing is essential for optimizing the performance and longevity of your pneumatic systems. Each material offers distinct advantages and can cater to specific industrial requirements, enabling you to find the exact match for your operational needs.
By selecting the appropriate tubing, you can ensure that your systems are efficient, reliable, and tailored to withstand any environmental challenges. Find the best selection of Parker pneumatic tubing at Hyspeco. We can help you equip your system with the correct components to run effectively and efficiently.