10 Tips for Attaching Hydraulic Hose Fittings
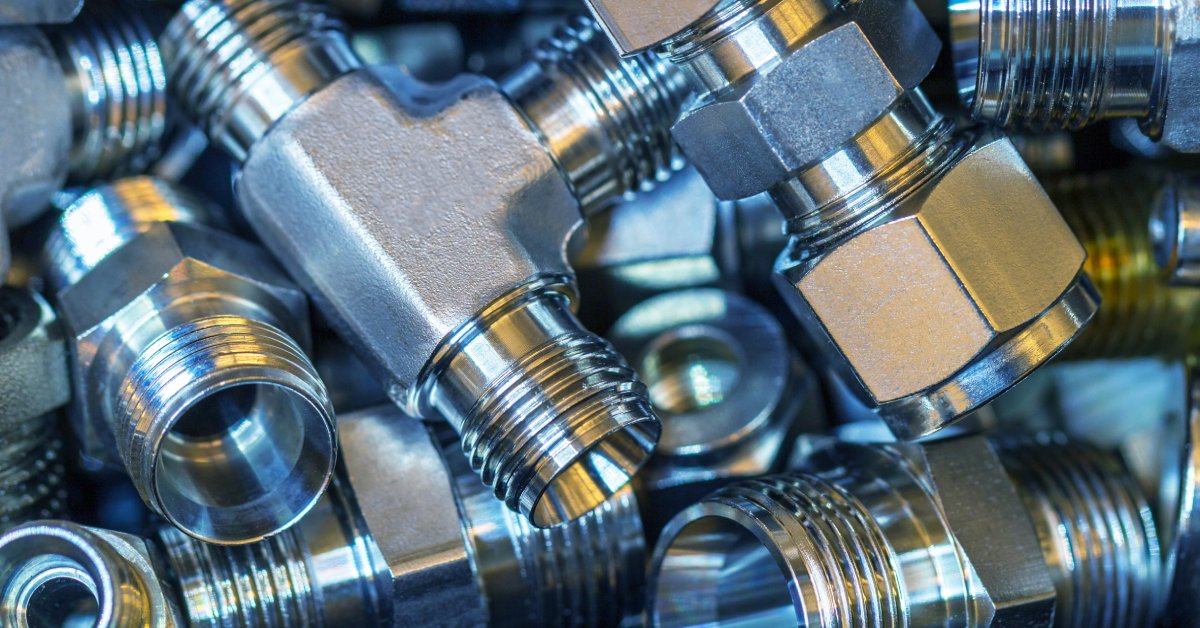
Hydraulic systems are essential in various industries, from construction to manufacturing. The integrity of these systems heavily relies on the proper attachment of hydraulic hose fittings. Incorrectly attached fittings can lead to leaks, equipment failure, and costly downtime.
Whether you’re working on heavy machinery or a simple hydraulic project, understanding the nuances of attaching fittings can significantly impact your results. To help ensure your hydraulic systems operate efficiently and safely, Hyspeco has compiled these ten essential tips for attaching hydraulic hose fittings.
Choose the Right Fittings
Choosing the right hydraulic hose fittings is the foundation of a secure and efficient system. Before starting, ensure you have the correct fittings for your specific application. Consider factors such as pressure ratings, hose diameter, and the type of fluid being transported. For example, high-pressure systems typically require steel fittings, while lighter applications can use brass.
Additionally, the fitting type—whether crimp or push-on—should align with your operational needs. Using the right fittings helps prevent leaks and enhances system performance. Hydraulic adapters often play a role here, as they enable connections between hoses and fittings that would otherwise be incompatible. Adapters should be used judiciously to avoid flow restrictions or leaks.
Inspect Hoses and Fittings
Always conduct a thorough inspection of both hoses and fittings before attachment. Dust, dirt, and debris can compromise the integrity of the connection, leading to contamination and potential system failure. Pay special attention to the interior of the hose, as trapped particles can circulate within the system and cause damage.
Throughout your inspection, look for any signs of wear, cracks, or corrosion. If you find any defects, replace the components to avoid potential failures.
Cut Hoses Properly
Cutting your hoses properly when attaching a hydraulic fitting is a critical step you shouldn’t forget. Doing this prevents frayed or irregular edges on your hose that could potentially compromise the fitting’s ability to seal correctly.
When cutting hydraulic hoses, use a proper hose cutter to achieve a clean, straight cut. Avoid using blunt tools or saws, as these can damage the hose and lead to leaks. Before cutting, mark the hose at the desired length and use a steady hand to ensure precision. Properly preparing and cutting the hose enhances the performance and safety of your hydraulic system and prolongs the lifespan of the fittings and hoses.
Deburr and Clean the Cut Ends
After cutting, always inspect the cut end for any irregularities or debris and remove them before attaching the fitting. Deburring the edges of the hose removes any sharp bits that could compromise the fitting seal.
Additionally, clean the inside and outside of the hose ends to eliminate any contaminants that could cause issues during attachment. Forgetting this step may cause risk to the integrity of your hydraulic system when attaching the fitting.
Use the Right Assembly Tools
To achieve a secure connection, you must utilize the appropriate tools for attaching fittings. Using the wrong tools can cause damage, reducing the lifespan of the hose and fittings. The wrong tools can also compromise the seal quality and potentially cause leaks or equipment failure.
The tools you might need to use include wrenches and torque wrenches. Using the correct tools ensures that you apply the right amount of torque, reducing the risk of damaging the fittings. We recommend having your tools handy when you’re ready to start so that you can ensure a proper fit.
Follow Manufacturer Guidelines
Not every hose fitting will follow the same requirements. Therefore, it is crucial to refer to the manufacturer's guidelines for the specific fittings and hoses you're using. By adhering to these protocols, you reduce the risk of costly downtime and maintenance due to equipment malfunction.
These guidelines often include detailed instructions on how to attach the fittings correctly and the necessary torque specifications. Together, the guidelines are designed to optimize the performance and lifespan of your hydraulic systems. Accounting for the unique characteristics of the materials and components used, they help ensure that the fittings and hoses function accordingly under expected pressures and conditions.
Align Fittings Properly
Proper alignment is key to preventing kinking in hydraulic hoses. Misalignment can lead to stress on the hose and fittings, increasing the risk of leaks or failure. Ensure that the fittings are aligned correctly before tightening.
Carefully position the hose to follow a natural, unrestricted path, avoiding sharp bends or twists. This reduces strain and enhances the durability of the assembly. Take your time to ensure everything is straight before proceeding.
Tighten Gradually
When tightening the fittings, do so gradually and evenly. Over-tightening can damage the hose or fitting and lead to premature failure and leaks. If using a torque wrench, refer to the specified torque values. These values indicate the ideal level of tightness required to maintain a secure connection without causing damage.
Remember that different fitting materials and applications may have varying torque requirements. For instance, steel fittings often require higher torque levels than fittings made from other materials. Adhering to these specifications ensures a reliable connection that maintains system integrity.
Test for Leaks
Once the fittings are attached, it’s crucial to conduct a leak test. Conducting tests after installation helps ensure your system is ready for operation under real-world conditions. Perform regular pressure tests as part of your maintenance routine to catch issues early and maintain optimal performance.
Apply pressure to the system and check for any signs of leaks around the fittings. Use specialized pressure gauges and testing equipment to obtain accurate readings and identify areas requiring attention. If you detect any leaks, relieve the pressure and disassemble and inspect the components before reattaching.
Perform Regular Maintenance Checks
Finally, schedule regular maintenance checks for your hydraulic systems. Inspect hoses and fittings periodically for wear and tear and replace components as necessary. This maintenance should include periodic checks, cleaning, and component replacements as needed.
Preventative maintenance can significantly extend the life of your hydraulic system and prevent costly repairs. Don’t forget to record information such as installation dates, component specifications, maintenance activities, and any issues encountered. This data can inform future decisions and support compliance with industry regulations and standards.
Attaching hydraulic hose fittings may seem straightforward, but attention to detail is crucial for ensuring a safe and reliable hydraulic system. By following Hyspeco’s ten tips, you can minimize the risk of leaks and failures, ensuring your equipment operates smoothly. Proper installation and maintenance are key to maximizing the efficiency and longevity of your hydraulic systems.