The Main Uses for Different Types of Hydraulic Pumps
Hydraulic pumps are key components in various industrial systems, converting mechanical energy into hydraulic energy in order to drive a multitude of applications. However, not every pump is the same. It’s important to explore the main uses for different types of hydraulic pumps so that you can better understand which one is better fit for your specific application. Keep reading for an overview of the three main types of hydraulic pumps, key considerations to keep in mind when selecting a hydraulic pump, and maintenance tips to ensure longevity and efficiency.
Gear Pumps
Gear pumps are one of the most commonly used hydraulic pumps due to their simplicity and durability. They operate by using two meshing gears that create a vacuum, drawing hydraulic fluid into the pump and then pushing it out.
Main Uses and Industries
Gear pumps are widely used in various industries, including agriculture, construction, and manufacturing. They are particularly effective in applications requiring consistent and high-pressure fluid flow, such as in agricultural machinery, industrial lubrication systems, and hydraulic presses.
Advantages and Limitations
Advantages:
- Simple design and construction
- High reliability and durability
- Cost-effective
- Suitable for high-pressure applications
Limitations:
- Limited efficiency compared to other types of hydraulic pumps
- Can be noisy
- Wear and tear over time can decrease performance
Vane Pumps
Vane pumps use a rotor with movable vanes that alter the size of the chambers to facilitate the movement of hydraulic fluid. This type of pump is known for its smooth operation and ability to handle variable flow rates.
Main Uses and Industries
Vane pumps are commonly used in industrial applications that require a steady, low-noise operation. They are often found in injection molding machines, automotive transmissions, and power steering systems. Additionally, vane pumps are suitable for mobile equipment and aviation hydraulics.
Advantages and Limitations
Advantages:
- Smooth and quiet operation
- Handles variable flow rates effectively
- Good volumetric efficiency
- Compact design
Limitations:
- More complex than gear pumps, leading to higher maintenance requirements
- Sensitive to contamination
- May wear out faster in high-pressure applications compared to gear pumps
Piston Pumps
Piston pumps are highly efficient and capable of handling high-pressure applications. They use a series of pistons driven by a cam or swashplate mechanism to move hydraulic fluid. Piston pumps can be either axial or radial, depending on the orientation of the pistons.
Main Uses and Industries
Piston pumps are ideal for heavy-duty applications that require high pressure and precise control. They are widely used in construction equipment, hydraulic presses, and industrial machinery. Their ability to handle high pressures makes them suitable for aerospace and marine applications as well.
Advantages and Limitations
Advantages:
- High efficiency and performance
- Capable of handling high-pressure applications
- Suitable for precise control and variable flow rates
- Long service life with proper maintenance
Limitations:
- Costs more than gear and vane pumps
- Complex design requires skilled maintenance
- Sensitive to contamination
Key Considerations When Choosing a Hydraulic Pump
When selecting a hydraulic pump for your application, it’s important to consider several key factors to ensure optimal performance and longevity. Here is a list of critical considerations:
- Flow rate and pressure requirements: Determine the necessary flow rate (in gallons per minute or liters per minute) and pressure (in pounds per square inch or bar) for your specific application.
- Fluid type: Consider the type of hydraulic fluid to be used, as some pumps are more compatible with certain types of fluids, like synthetic, mineral-based, or water-based fluids.
- Efficiency: Assess the efficiency of the pump, particularly if energy savings and performance are important in your application.
- Operating environment: Account for environmental conditions such as temperature fluctuations, exposure to contaminants, and humidity levels where the pump will be used.
- Noise level: Evaluate the acceptable noise level for your operation, especially if the pump will be used in a noise-sensitive environment.
- Maintenance requirements: Consider the maintenance needs and the level of service that the pump requires. Then, choose a pump that aligns with the maintenance capabilities of your team.
- Cost: Balance the initial purchase cost with the expected lifespan and total cost of ownership by considering the maintenance, energy consumption, and potential downtime costs.
- Size and weight: Ensure the physical size and weight of the pump fits within the spatial constraints of your application.
- Compatibility with existing systems: Verify that the pump is compatible with your existing hydraulic systems and components, such as motors, valves, and reservoirs.
- Special features: Look for any special features required for your application, like variable flow rates, integrated control systems, or specific certifications (e.g., ATEX for hazardous environments).
Thoroughly evaluating these considerations will allow you to confidently select a hydraulic pump that not only meets the demands of your operation, but also enhances the efficiency and reliability of your hydraulic system.
Maintenance Tips for Hydraulic Pumps
Proper maintenance is crucial to ensure the longevity and performance of your hydraulic pumps. Here are some essential tips for maintaining a stable maintenance routine.
Regular Inspection and Fluid Checks
Routine inspections help identify potential issues before they escalate. Check your hydraulic pumps for leaks, unusual noises, and vibrations. Additionally, it’s important to regularly check and maintain hydraulic fluid levels, as low fluid can cause cavitation and damage to the pump.
Filter Replacement
Hydraulic systems are sensitive to contamination. Regularly replacing filters will help you keep the hydraulic fluid clean and free from debris, ensuring smooth operation and preventing damage to internal components.
Monitor Operating Temperatures
Excessive heat can reduce the efficiency and lifespan of hydraulic pumps. Monitor operating temperatures and ensure the system has adequate cooling mechanisms in place. If temperatures consistently exceed recommended levels, it’s necessary to investigate and address the underlying cause.
Lubrication and Seals
Proper lubrication is vital for the smooth operation of moving parts within the pump. Ensure all lubrication points are adequately serviced. Additionally, inspecting and replacing seals as needed will help you prevent leaks and maintain the pressure integrity of your systems.
Professional Servicing
When in doubt or when complex maintenance tasks arise, consult a professional hydraulic technician. Regular professional servicing can help detect and address issues that may not be apparent during routine inspections.
Understanding the main uses for different types of hydraulic pumps enables manufacturers, engineers, and other industry professionals to make informed decisions that are tailored to their specific needs. From the simplicity and reliability of gear pumps, the smooth operation of vane pumps, and the high efficiency of piston pumps, each type of hydraulic pump offers unique advantages and limitations when considering the proper pump required for your application.
Whether you’re replacing a pump or building a new system, don’t forget to browse Hyspeco’s Parker hydraulic pumps. We have various types of pumps that work seamlessly with different applications. Browse our collection to find what you’re looking for, or give us a call to speak with one of our industry professionals for additional assistance.
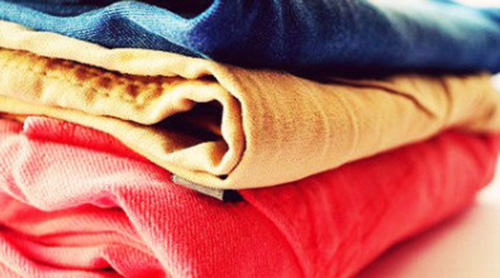
Lorem Ipsum is simply dummy text of the printing and typesetting industry. Lorem Ipsum has been the industry's standard dummy text ever since the 1500s, when an unknown printer took a galley of type and scrambled it to make a type specimen book.