Pneumatic Valves 101: What Are the Different Types?
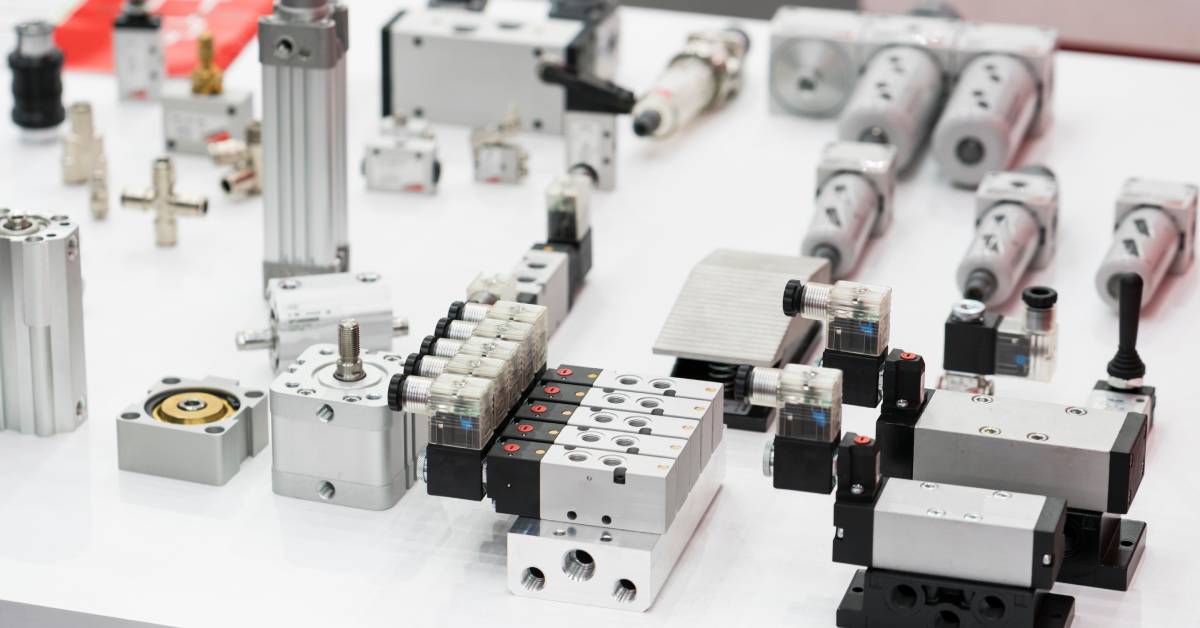
At the heart of any pneumatic system lies components that dictate the flow and direction of power. These tiny but powerful parts are called pneumatic valves. They come in a variety of forms, each serving a unique purpose and dictating the efficiency and success of an entire operation. You can ensure your system has the exact flow expertise it requires by learning more about the different types of pneumatic valves. We’ll go over everything you need to know to equip your systems with the best components.
What Are Pneumatic Valves?
Pneumatic valves are essential components within pneumatic systems that are responsible for regulating the passage of air or gas to control the direction, pressure, and flow rate of your pneumatic system. They function by opening, closing, or partially obstructing the pathways through which the air travels.
Typically, a system can operate pneumatic valves manually, automatically, or via an external signal, such as an electrical input or pressure sensor. The ability to swiftly and precisely control airflow allows these valves to power a wide range of equipment, from simple tools to complex industrial machinery.
Configurations for Pneumatic Valves
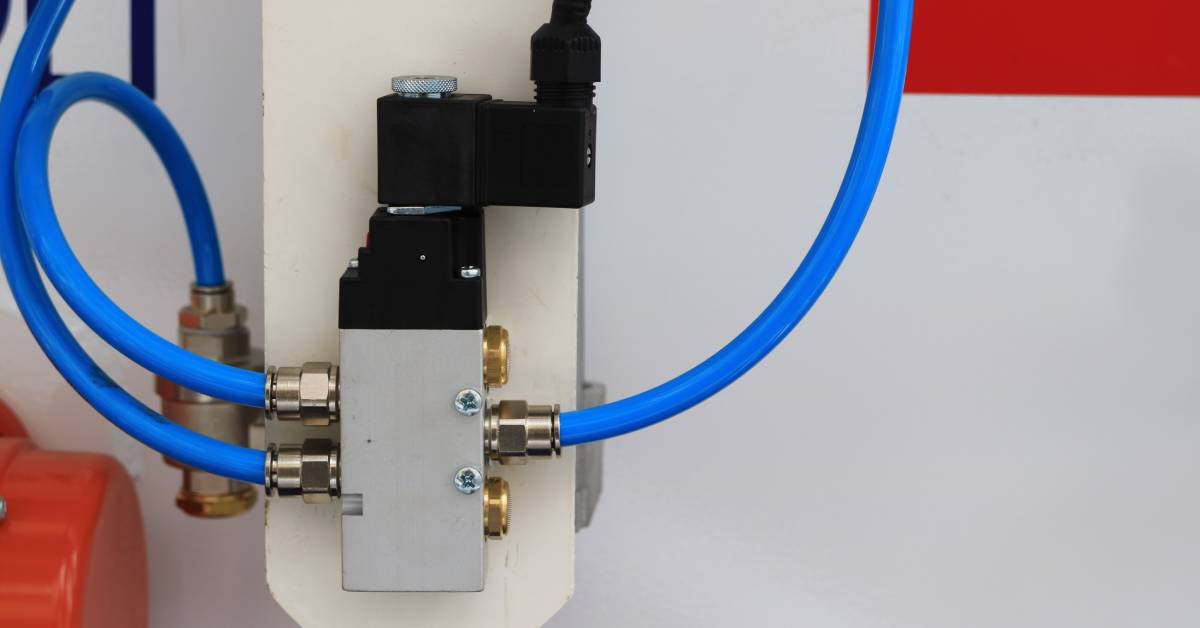
There are several configurations for pneumatic valves, each designed to meet the specific needs of different systems. Understanding these configurations is key to selecting the right valve for your application.
Number of Switching Positions
Pneumatic valves can have different switching positions, typically from two to five positions. These positions determine how the valve directs the flow of air through the system.
Mechanisms Applied To Open and Close Ports
There are various mechanisms used to open or close the valve ports, including manual levers, solenoids, air-actuated pistons, or spring returns. These mechanisms determine how the valve switches between its positions.
Number of Inlet and Outlet Ports
Valves vary in the number of inlet and outlet ports they contain. Common configurations include two-way, three-way, and four-way valves, which indicate the number of pathways available for air to enter or exit.
Status of the Valve When in the Un-Actuated State
We categorize valves based on their status when they are not actuated. For example, a normally closed valve halts airflow until activated, while a normally open valve allows airflow until it shuts off.
Each configuration offers different operational characteristics, helping to tailor pneumatic systems for specific applications or performance requirements.
Primary Types of Pneumatic Valves
Understanding the primary types of pneumatic valves is essential for anyone involved in designing or maintaining pneumatic systems. Each type serves a specific purpose and offers unique benefits based on its design and functionality.
Two-Way Valves
Two-way valves have two ports and can start or stop the flow of air. They function like a simple on/off switch, making them ideal for applications requiring straightforward control. These valves are common in systems where you need basic airflow regulation.
Three-Way Valves
The design of three-way valves alternates airflow between two pathways. They are perfect for applications that require a mechanism to divert airflow, such as switching between vacuum and pressure functions.
Four-Way Valves
Four-way valves, equipped with four ports, control the direction of airflow in double-acting cylinders. These valves are vital in applications requiring forward and reverse motion, providing precise control over complex movements.
Spring Offset Valves
Spring offset valves use a spring mechanism to return the valve to its default position when they are not actuated. This feature ensures the safety and reliability of your systems, making them a popular choice in systems requiring fail-safe operations.
Pneumatic Valves Based on Actuators
Actuators play a crucial role in determining how pneumatic valves operate. Different types of actuators offer varying levels of control and automation, impacting the overall performance of the system.
Solenoid Valves
Solenoid valves use an electromagnetic coil to move the valve. Their rapid response time and precise control make them ideal for automated systems. Solenoid valves are common in applications that require remote operation.
Air-Operated Valves
Air-operated valves, also known as pneumatically actuated valves, use air pressure to open and close. These valves are suitable for hazardous environments where electrical actuation is not feasible. They offer a reliable solution for systems requiring simple yet effective control.
Mechanical Valves
Mechanical valves rely on physical force to actuate. You’ll often see them in applications that require human intervention, such as emergency shut-off systems. Mechanical valves provide a straightforward and cost-effective solution for basic operations.
3/2 Valves
3/2 valves, featuring three ports and two positions, are versatile components used to control the flow of air in both supply and exhaust functions. They are particularly useful in applications that require compact and efficient control.
Choosing a Valve for Your Application
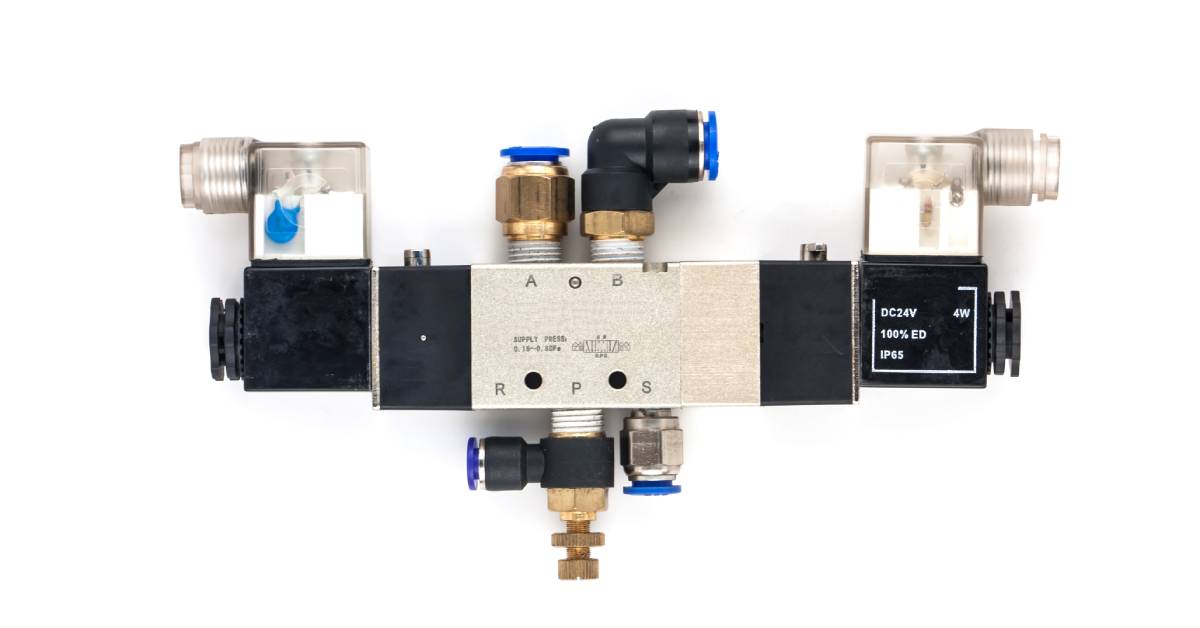
Choosing the right pneumatic valve for your application is crucial to ensure optimal system performance and reliability. Here are some tips to guide your decision-making process.
Understand the System Requirements
Begin by identifying the specific needs of your application. This could include the operating pressure, the required flow rate, and the type of media (e.g., air, gases) used. This will narrow down the valve types that are appropriate for your system.
Consider the Actuation Method
Decide on the most suitable actuation method based on your system’s environment and automation needs. Choose solenoid valves for applications requiring fast and precise control, air-operated valves for environments where electrical components are unsafe, and mechanical valves for manual operations.
Evaluate Environmental Conditions
Assess the operating environment, including temperature, humidity, and exposure to contaminants, as these factors can influence valve performance. Select a valve constructed from materials that are resistant to your specific environmental conditions in order to ensure durability.
Prioritize Maintenance and Accessibility
Choose valves that are easy to maintain and access, especially if you expect regular upkeep. This can reduce downtime and ensure efficient system operations.
Consider Safety and Compliance
Ensure that the valve meets any relevant safety standards and certifications required for your industry or application. Valves with fail-safe features, such as spring offset mechanisms, can enhance operator safety and system integrity.
Economic Considerations
Balance the cost of the valve with its features and lifespan. While cheaper options may seem attractive at first, investing in a high-quality valve may reduce long-term maintenance costs and improve your overall system efficiency.
By carefully weighing these factors, you can select the best valve for your application, achieving enhanced operations and durability in your pneumatic systems.
Understanding the different types of pneumatic valves is critical for optimizing the performance and reliability of your pneumatic systems. By selecting the most suitable valve configurations and actuator types for your specific application, you can ensure efficient and safe operations.
At Hyspeco, we offer a comprehensive range of high-quality Parker pneumatic valves and components tailored to meet diverse industrial needs. Our team of experts is ready to help you navigate the complexities of your pneumatic systems in order to find your perfect solution. Trust Hyspeco for your next purchase, and experience the difference that exceptional products and knowledgeable support can make in your projects.